干懸浮劑的連續(xù)流化床造丸法研究與實踐
來源:《中國飼料添加劑》2020年第9期(總第221期)時間:2020-10-18
摘要:對干懸浮劑的性能影響因素,包括微觀粒徑、微觀粒子的助劑包覆原理、粒子干燥過程的受熱原理進(jìn)行分析,結(jié)合連續(xù)流化床造丸的原理研究與實踐,得出連續(xù)流化床造丸方法是比較適合的,其工藝路線為濕法砂磨粉碎-微米級粒子液態(tài)包覆-微米級液滴霧化-單微粒包覆-層疊造粒-連續(xù)干燥成有大量微細(xì)毛孔的顆粒,實現(xiàn)潤濕性、高強度、分散性、懸浮率、熱貯性、流動性、無粉塵性能指標(biāo)的提高;有助于助劑用量的下降、采用低溫型助劑,降低制劑成本;與傳統(tǒng)噴塔法比較,因熱能損失小,運行成本低于噴塔法10-20%;結(jié)合環(huán)保和安全因素,綜合成本有望于接近傳統(tǒng)干法造粒法;考慮藥效提高、可加工水溶性和低融點物料,優(yōu)勢更明顯。關(guān)鍵詞:干懸浮劑1;噴霧干燥2;顆粒形態(tài)3;連續(xù)流化床造丸粒4;
水分散粒劑是比較理想的顆粒劑,從上世紀(jì)出現(xiàn),經(jīng)過廣泛推廣、充分顯示出生命力,尤其是現(xiàn)代人們的環(huán)保意識愈來愈強、應(yīng)用市場越來越廣,對高效低毒藥劑的要求越來越高,目前許多公司都在致力于研究開發(fā)新的水分散粒劑,水分散粒劑是很好的劑型,傳統(tǒng)的干法粉碎主要是加工細(xì)度達(dá)不到要求,粉碎和造粒工序不能實現(xiàn)連續(xù)化生產(chǎn),致使粉塵飛揚比較大、物料損耗和環(huán)保都是問題, 本世紀(jì)在水分散粒劑的基礎(chǔ)上,國內(nèi)開發(fā)應(yīng)用了干懸浮劑,顯示出了藥效提高、使用方便等各種優(yōu)點,經(jīng)過幾年應(yīng)用,發(fā)現(xiàn)存在水溶性物料和低融點物料很難制備、助劑使用量偏大導(dǎo)致制劑成本高、成品存在潤濕性不好和強度低問題、噴塔干燥方法能耗大等瓶頸,導(dǎo)致無法大規(guī)模應(yīng)用為主導(dǎo)劑型,目前僅約占5%的市場規(guī)模,同時還存在類似可濕粉的分散性差、結(jié)塊、流動性差、粉塵飛揚、靜電性、粘壁、熱貯性不好等缺點,目前干懸浮劑已經(jīng)在多行業(yè)大量使用。
- 干懸浮劑的制備原理和現(xiàn)有不足
干法粉碎法的超微粉碎可滿足要求,粉碎的粒徑小了比表面積增大,粉劑過于蓬松不好使用,這樣就需要加工成粒劑,助劑在包覆前,微粉粒之間已存在絮結(jié)的可能性,加之微粉粒不圓整,導(dǎo)致藥效降低和懸浮率降低。
干懸浮劑的噴塔制備法,采用了濕法砂磨、液態(tài)中微粉粒絮結(jié)可能性小,但霧化液滴包含數(shù)十萬個微粉粒、互相靠緊、干燥后微粉粒之間沒有孔隙、此時微粉粒絮結(jié)可能性就增大,并且噴塔的方法決定了進(jìn)風(fēng)溫度和料層溫度通常比較高,而目前助劑在使用過程中發(fā)現(xiàn)極易受高溫影響,導(dǎo)致助劑廠家配方存有難度,崩解、懸浮、熱貯都存在間接的問題。
- 干懸浮劑的制備要點
行業(yè)內(nèi)各項研究發(fā)現(xiàn),當(dāng)微粉粒小于1200目、起碼小于3um、并且為單獨存在時,對藥劑的藥效是好的,在懸浮液中的絮結(jié)可能性小、不易發(fā)生沉淀,可有更好的藥效、具有保證懸浮率的基礎(chǔ)條件。
2.2助劑配方。
干懸浮劑加工的關(guān)鍵技術(shù)是要防止微粉粒在包覆、干燥、造粒過程中、成品貯存期間,粉粒重新絮結(jié)成粗粉粒,因而在配方中要使用一種叫隔離劑的助劑,它能將微粉粒隔離開來,當(dāng)粉粒重新絮結(jié)成粗粉?;蛑鷦┟撀鋾r就形成死顆粒,所以要求微粉粒絮結(jié)率低、助劑脫落率低、成品流動性能好、無粉塵飛揚;入水后,自動崩解,分散成懸浮液;要求潤濕性好、分散性好、懸浮率高、穩(wěn)定性好;同時制劑和加工成本要具備性價比的大生產(chǎn)可行性。
優(yōu)良助劑配方工藝是保證隔離、分散、懸浮、熱貯等性能的要點之一,另外制備溫度也是要素之一,制備溫度經(jīng)常影響助劑是否能用、和用量的大小,噴塔方法就是直觀的體現(xiàn),經(jīng)常發(fā)生溫度超過一個值1度時,就會導(dǎo)致成品不合格,而高溫型的助劑成本又大大提高、甚至難以開發(fā)成功。
2.3助劑隔離方式。
分析發(fā)現(xiàn)好隔離方式是實現(xiàn)助劑在單微粉粒表面包覆,形成獨立的單包覆微粉粒,從而阻止微粉粒絮結(jié),同時微粉粒的形態(tài)需要圓整,避免形成菱角、造成包覆不全或包覆助劑量增大。
包覆后的若干個微??蛇M(jìn)行分層造粒、形成具有一定強度的顆粒、解決了粉劑的缺點,同時微粉粒之間需要有一定間隙、避免靠的太近即存在微孔,作用就是防止微粉?;ハ嘈踅Y(jié)特別是受熱絮結(jié)、散熱、透水,才可輔助實現(xiàn)好的分散性、懸浮率、熱貯性。
2.4干燥方式。
分析發(fā)現(xiàn)目前助劑的耐溫性,瞬間耐溫常處于100-150度,長時間耐溫性常處于50-80度,越是高溫型的助劑成本越大。
包覆后的若干個微粒進(jìn)行造粒時,為了避免噴塔方法液滴的外高溫、內(nèi)低溫的不利現(xiàn)象,采用低溫干燥方式,可接近于熱貯溫度,同時采用分層包覆造粒、從小到大的長大方式,讓每個顆粒內(nèi)的每個微粉粒受熱條件一致,避免形成死顆粒、保持好懸浮率。
2.5 成品形態(tài)
分析統(tǒng)計發(fā)現(xiàn)好成品顆粒徑是30-80目,要有一定強度、不易破碎,避免顆粒過小造成粉塵飛揚、結(jié)塊、入水成團(tuán),避免顆粒太大造成入水太快、分散慢,顆粒越是接近于球形、商品的外觀價值越好。
2.6 生產(chǎn)方式。
只有連續(xù)性生產(chǎn),才能具備工藝參數(shù)重復(fù)性、產(chǎn)品質(zhì)量穩(wěn)定、降低勞動強度、降低能耗和穩(wěn)定生產(chǎn)。
只有封閉性生產(chǎn),才能具備無粉塵性、環(huán)保和安全性。
- 干懸浮劑的連續(xù)流化床造粒方法分析
工藝方框流程圖,如圖1。
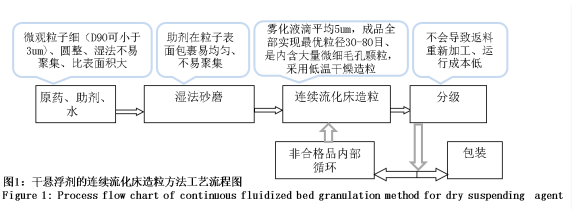
工藝路線:砂磨粉碎得到圓整的微粉粒,并且是與助劑、水同時砂磨,形成微米級粒子的乳化液即包覆液;通過連續(xù)流化床造粒機的霧化噴槍形成微米級液滴霧化、平均液滴直徑可達(dá)5um,形成單微粒包覆,并且每個微粉子表面都是涂滿助劑的;此時單液滴需要一定的初步干燥時間形成單微粒包覆烘干,并且需要控制干燥程度,太干了微粉粒之間不好粘附造粒,太濕了會形成實心和絮結(jié)可能,初步干燥后的微粉粒粘附到晶種表面后,吸收晶種的熱量進(jìn)一步干燥,此時會有一定的鋪展作用;無數(shù)個單液滴周爾復(fù)始,形成層疊包覆造粒,最終形成有大量微細(xì)毛孔的成品顆粒;在此過程中,可以看出采用頂噴是比較佳的方式,因為側(cè)噴和底噴霧化液滴會直接噴到晶種表面、行程短并且無法調(diào)節(jié),易形成涂層、鋪展的效果,頂噴會給單液滴一定的預(yù)干燥時間,并且可適當(dāng)調(diào)節(jié),形成有合適的、大量微細(xì)毛孔的成品好形態(tài)顆粒。
3.2連續(xù)流化床造粒方法原理說明分析
微粉粒到成品顆粒的原理說明,如圖2。
原理分析:砂磨粉碎-微米級粒子和乳化-微米級液滴霧化-單微粒包覆和預(yù)烘干-層疊包覆造粒-低溫連續(xù)干燥成有大量微細(xì)毛孔的顆粒,結(jié)合低溫操作和大量微細(xì)毛孔的存在,可讓成品顆粒性能實現(xiàn)完美。
3.3連續(xù)流化床造粒方法效果分析
3.3.1 微觀粒子直徑
砂磨粉碎可得到圓整的微粉粒,粒徑可實現(xiàn)小于3um的理想粒徑,為濕法粉碎,無粉塵飛揚,并且是與助劑、水同時砂磨,可直接一步形成微米級粒子的乳化液即包覆液,此時避免了干微粉粒的初始絮結(jié)。
3.3.2 助劑
連續(xù)流化床造丸的優(yōu)點是進(jìn)風(fēng)和料層溫度不需要傳統(tǒng)噴塔那么高,溫度可隨意調(diào)節(jié)、采用低溫,即不需要采用難以開發(fā)和高成本的高溫型助劑,可非常好的適應(yīng)現(xiàn)有助劑種類。
通過微米級的單液滴霧化、初始干燥和最終含有大量微細(xì)毛孔的顆粒結(jié)構(gòu),讓助劑用量下降,經(jīng)過分析統(tǒng)計,約可下降用量30%;大量微細(xì)毛孔的存在讓微粉粒在固態(tài)時的絮結(jié)可能性變小,從而成品的熱貯性變好,又進(jìn)一步為下降助劑用量提供可能性。
結(jié)合以上,看出可降低干懸浮劑的制劑成本,為廣泛推廣應(yīng)用創(chuàng)造了可行性條件。
3.3.3 助劑隔離方式
通過微米級的單液滴霧化、初始干燥,實現(xiàn)助劑在單微粉粒表面包覆,形成比較佳的獨立單包覆微粉粒效果;包覆后的若干個微??蛇M(jìn)行分層造粒、形成具有一定強度的成品顆粒,通過頂噴流化床形成含有大量微細(xì)毛孔的顆粒結(jié)構(gòu),這是比較佳成品結(jié)構(gòu);綜合形成了比較佳助劑隔離方式。
3.3.4 干燥方式
連續(xù)流化床造丸的優(yōu)點是進(jìn)風(fēng)和料層溫度不需要傳統(tǒng)噴塔那么高,溫度可隨意調(diào)節(jié)、采用低溫,加上優(yōu)化的頂噴霧化造粒的智能化效果,顆粒越大長的越慢,顆粒越小長的越快,用分層包覆造粒、從小到大的長大方式,讓每個顆粒內(nèi)的每個微粉粒受熱條件一致,避免了形成死顆粒、保持理想懸浮率。與傳統(tǒng)噴塔法比較,因熱能損失小,運行成本低于噴塔法10-20%。
連續(xù)流化床造丸可具備連續(xù)性生產(chǎn)和封閉性生產(chǎn)的技術(shù)條件,結(jié)合環(huán)保和安全因素,綜合成本有望于接近傳統(tǒng)干法造粒法。
3.3.5 成品形態(tài)
可實現(xiàn)成品全部為30-80目的類球形顆粒、粒徑可調(diào),經(jīng)多品種物料的驗證,實現(xiàn)了快速潤濕性、高強度、并有助于藥效、分散性、懸浮率、熱貯性、環(huán)保性、無粉塵性能指標(biāo)的多面提高。
3.4頂噴連續(xù)流化床造丸應(yīng)用實例分析
應(yīng)用物料舉例,如圖3。
常見性能:潤濕性試驗?zāi)壳熬鶎崿F(xiàn)秒潤、基本完全懸浮、整體性能多面提升,商品外觀為類球形顆粒、價值增高。
因其具有的單微粉粒包覆和大量微細(xì)毛孔結(jié)構(gòu),進(jìn)一步增加了制劑的藥效、可加工水溶性和低融點物料。
干懸浮劑的噴霧造粒和連續(xù)流化床造粒微觀對比,如圖4。 連續(xù)流化床干懸浮劑其余應(yīng)用物料舉例,如圖5。 4 結(jié) 論
本文對干懸浮劑的性能影響因素,包括微觀粒徑、助劑配方、助劑隔離方式、微觀粒子的助劑包覆原理、粒子干燥過程的受熱原理進(jìn)行綜合分析,結(jié)合連續(xù)流化床造丸的原理研究與實踐,得出頂噴式連續(xù)流化床造丸方法是比較適合的,其工藝路線為濕法砂磨粉碎-微米級粒子液態(tài)包覆-微米級液滴霧化-單微粒包覆預(yù)干燥-層疊造粒-連續(xù)干燥成有大量微細(xì)毛孔的顆粒,實現(xiàn)潤濕性、高強度、分散性、懸浮率、熱貯性、流動性、無粉塵性能指標(biāo)的多面提高;有助于助劑用量的下降、采用低溫型助劑,降低制劑成本;與傳統(tǒng)噴塔法比較,因熱能損失小,運行成本低于噴塔法10-20%;結(jié)合環(huán)保和安全因素,綜合成本有望于接近傳統(tǒng)干法造粒法;考慮藥效提高、可加工水溶性和低融點物料,優(yōu)勢更明顯;已完全具備水分散粒劑的主導(dǎo)加工工藝的可能性。
參考文獻(xiàn):
[1]徐蓮英 侯世祥.中藥制藥工藝技術(shù)解析.ISBN7-117-05735-1/R.5736 人民衛(wèi)生出版社,2003.
[2]王喜忠,于才淵 ,周才君.噴霧干燥[M].北京:化學(xué)工業(yè)出版社,2003.
[3]陳林書,王新月.賴氨酸硫酸鹽類產(chǎn)品應(yīng)用噴霧流化床造粒得到的顆粒形態(tài)分析展望[J] .中國飼料添加劑, 2012, 124(10): 32-34.
[4]陳林書.連續(xù)噴霧流化床造丸包衣在精細(xì)化工飼料行業(yè)的應(yīng)用和開發(fā)[J] .中國飼料添加劑, 2015,(1): 39-42.
本文章僅是摘錄于相關(guān)文章,具體以相關(guān)文章刊登的原記錄為準(zhǔn),版權(quán)歸作者所有。